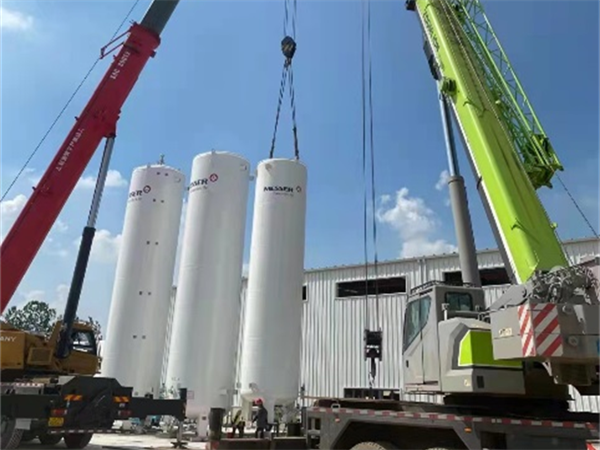
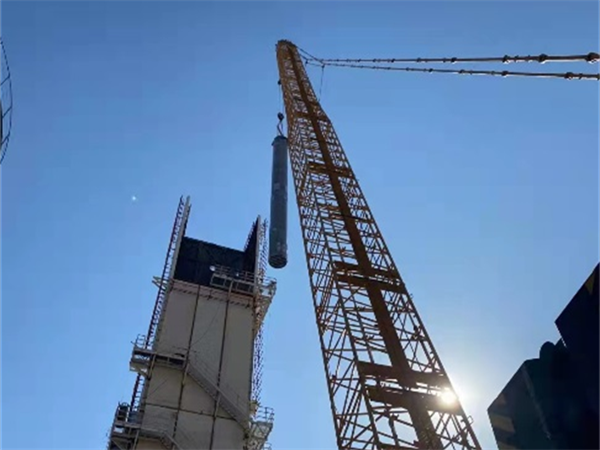
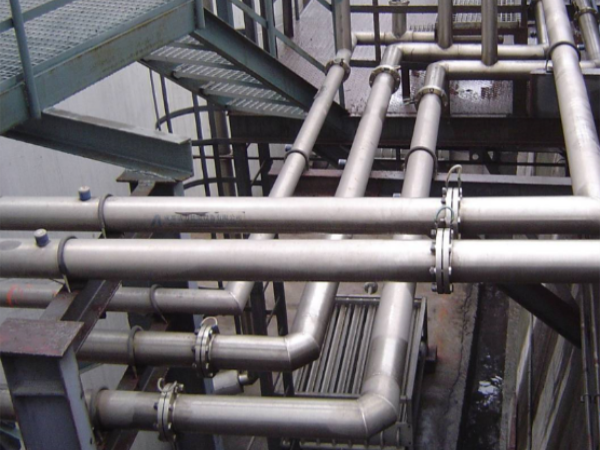
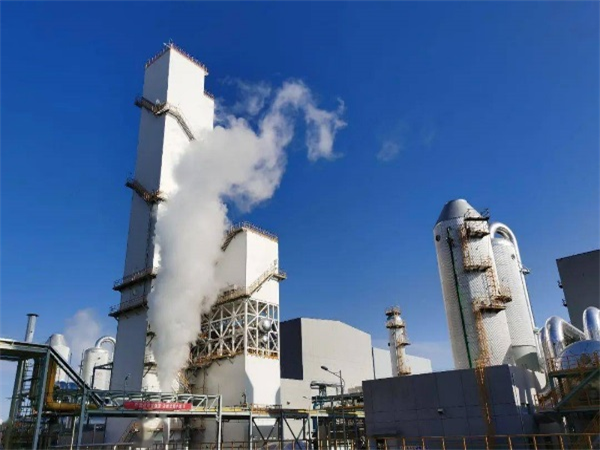
With the rapid expansion of the company's production scale in recent years, the oxygen consumption for steelmaking continues to increase, and the requirements for the reliability and economy of oxygen supply are higher and higher. There are two sets of small-scale oxygen production systems in the oxygen production workshop, the maximum oxygen production is only 800 m3/h, which is difficult to meet the oxygen demand at the peak of steelmaking. Insufficient oxygen pressure and flow often occur. During the interval of steelmaking, a large amount of oxygen can only be emptied, which not only does not adapt to the current production mode, but also causes high oxygen consumption cost, and does not meet the requirements of energy conservation, consumption reduction, cost reduction and efficiency increase, therefore, the existing oxygen generation system needs to be improved.
Liquid oxygen supply is to change the stored liquid oxygen into oxygen after pressurization and vaporization. Under standard state, 1 m³ liquid oxygen can be vaporized into 800 m3 oxygen. As a new oxygen supply process, compared with the existing oxygen production system in the oxygen production workshop, it has the following obvious advantages:
1. The system can be started and stopped at any time, which is suitable for the current production mode of the company.
2. The oxygen supply of the system can be adjusted in real time according to the demand, with sufficient flow and stable pressure.
3. The system has the advantages of simple process, small loss, convenient operation and maintenance and low oxygen production cost.
4. The purity of oxygen can reach more than 99%, which is conducive to reducing the amount of oxygen.
Process and Composition of Liquid Oxygen Supply System
The system mainly supplies oxygen for steelmaking in steelmaking company and oxygen for gas cutting in forging company. The latter uses less oxygen and can be ignored. The main oxygen consumption equipment of the steelmaking company is two electric arc furnaces and two refining furnaces, which use oxygen intermittently. According to statistics, during the peak of steelmaking, the maximum oxygen consumption is ≥ 2000 m3 / h, the duration of maximum oxygen consumption, and the dynamic oxygen pressure in front of the furnace is required to be ≥ 2000 m³/h.
The two key parameters of liquid oxygen capacity and maximum oxygen supply per hour shall be determined for the type selection of the system. On the premise of comprehensive consideration of rationality, economy, stability and safety, the liquid oxygen capacity of the system is determined to be 50 m³ and the maximum oxygen supply is 3000 m³ / h. therefore, the process and composition of the whole system are designed, Then the system is optimized on the basis of making full use of the original equipment.
1. Liquid oxygen storage tank
The liquid oxygen storage tank stores liquid oxygen at - 183 ℃ and is the gas source of the whole system. The structure adopts the vertical double-layer vacuum powder insulation form, with small floor area and good insulation performance. The design pressure of the storage tank, effective volume of 50 m³, normal working pressure - and working liquid level of 10 m³-40 m³. The liquid filling port at the bottom of the storage tank is designed according to the on-board filling standard, and the liquid oxygen is filled by the external tank truck.
2. Liquid oxygen pump
The liquid oxygen pump pressurizes the liquid oxygen in the storage tank and sends it to the carburetor. It is the only power unit in the system. In order to ensure the reliable operation of the system and meet the needs of start and stop at any time, two identical liquid oxygen pumps are configured, one for use and one for standby. The liquid oxygen pump adopts horizontal piston cryogenic pump to adapt to the working conditions of small flow and high pressure, with working flow of 2000-4000 L/h and outlet pressure, The working frequency of the pump can be set in real time according to the oxygen demand, and the oxygen supply of the system can be adjusted by adjusting the pressure and flow at the pump outlet.
3. Vaporizer
The vaporizer adopts air bath vaporizer, also known as air temperature vaporizer, which is a star finned tube structure. The liquid oxygen is vaporized into normal temperature oxygen by natural convection heating of air. The system is equipped with two vaporizers. Normally, one vaporizer is used. When the temperature is low and the vaporization capacity of a single vaporizer is insufficient, the two vaporizers can be switched or used at the same time to ensure sufficient oxygen supply.
4. Air storage tank
The air storage tank stores vaporized oxygen as the storage and buffer device of the system, which can supplement the instantaneous oxygen supply and balance the pressure of the system to avoid fluctuation and impact. The system shares a set of gas storage tank and main oxygen supply pipeline with the standby oxygen generation system, making full use of the original equipment. The maximum gas storage pressure and maximum gas storage capacity of the gas storage tank are 250 m³. In order to increase the air supply flow, the diameter of the main oxygen supply pipe from the carburetor to the air storage tank is changed from DN65 to DN100 to ensure sufficient oxygen supply capacity of the system.
5. Pressure regulating device
Two sets of pressure regulating devices are set in the system. The first set is the pressure regulating device of liquid oxygen storage tank. A small part of liquid oxygen is vaporized by a small carburetor at the bottom of the storage tank and enters the gas phase part in the storage tank through the top of the storage tank. The return pipeline of liquid oxygen pump also returns a part of gas-liquid mixture to the storage tank, so as to adjust the working pressure of the storage tank and improve the liquid outlet environment. The second set is the oxygen supply pressure regulating device, which uses the pressure regulating valve at the air outlet of the original gas storage tank to adjust the pressure in the main oxygen supply pipeline according to the oxygen demand.
6. Safety device
The liquid oxygen supply system is equipped with multiple safety devices. The storage tank is equipped with pressure and liquid level indicators, and the outlet pipeline of liquid oxygen pump is equipped with pressure indicators to facilitate the operator to monitor the system status at any time. Temperature and pressure sensors are set on the intermediate pipeline from the carburetor to the air storage tank, which can feed back the pressure and temperature signals of the system and participate in the system control. When the oxygen temperature is too low or the pressure is too high, the system will automatically stop to prevent accidents caused by low temperature and overpressure. Each pipeline of the system is equipped with safety valve, vent valve, check valve, etc., which effectively ensures the safe and reliable operation of the system.
Operation and Maintenance of Liquid Oxygen Supply System
As a low-temperature pressure system, liquid oxygen supply system has strict operation and maintenance procedures. Misoperation and improper maintenance will lead to serious accidents. Therefore, special attention should be paid to the safe use and maintenance of the system.
The operation and maintenance personnel of the system can only take the post after special training. They must master the composition and characteristics of the system, be familiar with the operation of various parts of the system and the safety operation regulations.
Liquid oxygen storage tank, vaporizer and gas storage tank are pressure vessels, which can only be used after obtaining the special equipment use certificate from the local bureau of technology and quality supervision. The pressure gauge and safety valve in the system must be submitted for inspection regularly, and the stop valve and indicating instrument on the pipeline should be inspected regularly for sensitivity and reliability.
The thermal insulation performance of the liquid oxygen storage tank depends on the vacuum degree of the interlayer between the inner and outer cylinders of the storage tank. Once the vacuum degree is damaged, the liquid oxygen will rise and expand rapidly. Therefore, when the vacuum degree is not damaged or it is not necessary to fill pearlite sand to vacuum again, it is strictly prohibited to disassemble the vacuum valve of the storage tank. During use, the vacuum performance of the liquid oxygen storage tank can be estimated by observing the volatilization amount of liquid oxygen.
During the use of the system, a regular patrol inspection system shall be established to monitor and record the pressure, liquid level, temperature and other key parameters of the system in real time, understand the change trend of the system, and timely notify professional technicians to deal with abnormal problems.
Post time: Dec-02-2021